A wiring harness manufacturer is a company that specializes in designing, producing, and assembling wiring harnesses. Wiring harnesses are essential components in many industries, including automotive, aerospace, and telecommunications. They are used to organize and protect electrical wires and cables, and they help to ensure that electrical systems function properly.
There are many benefits to using wiring harnesses. They can help to reduce the risk of electrical fires, improve the reliability of electrical systems, and make it easier to troubleshoot and repair electrical problems. Wiring harnesses can also help to reduce the weight and cost of electrical systems.
The history of wiring harness manufacturing dates back to the early days of the automotive industry. As cars became more complex, the need for organized and protected electrical systems grew. The first wiring harnesses were simple affairs, but they have become increasingly sophisticated over time. Today, wiring harnesses are used in a wide variety of applications, from cars and trucks to airplanes and spacecraft.
The main article topics that will be covered in this article include:
- The different types of wiring harnesses
- The materials used to make wiring harnesses
- The process of manufacturing wiring harnesses
- The benefits of using wiring harnesses
- The future of wiring harness manufacturing
Wiring Harness Manufacturer
A wiring harness manufacturer plays a crucial role in various industries, ensuring the efficient functioning of electrical systems through the production of essential components known as wiring harnesses. These manufacturers specialize in designing, producing, and assembling these harnesses, adhering to specific requirements and standards.
- Quality: Renowned manufacturers prioritize the production of high-quality wiring harnesses, ensuring durability and reliability.
- Customization: They offer customized solutions tailored to specific customer needs and project requirements.
- Expertise: Experienced manufacturers possess in-depth knowledge and expertise in harness design, material selection, and manufacturing processes.
- Technology: Advanced manufacturers employ cutting-edge technology and equipment to ensure precision and efficiency in production.
- Efficiency: Streamlined manufacturing processes and optimized designs contribute to efficient production and cost-effectiveness.
- Compliance: Reputable manufacturers adhere to industry standards and regulations, ensuring compliance and safety.
These key aspects collectively contribute to the significance of wiring harness manufacturers in diverse industries. Their expertise and commitment to quality ensure the reliable functioning of electrical systems in applications ranging from automotive and aerospace to telecommunications and industrial machinery. By understanding these essential aspects, we gain a deeper appreciation for the role of wiring harness manufacturers in shaping the performance and safety of modern technologies.
Quality
The production of high-quality wiring harnesses is a cornerstone of the wiring harness manufacturing industry. Renowned manufacturers recognize the critical role of quality in ensuring the durability and reliability of these essential components. By prioritizing quality, they establish a solid foundation for the performance and safety of electrical systems in various applications.
The durability of wiring harnesses is a crucial factor, particularly in demanding environments. High-quality materials and meticulous manufacturing processes contribute to harnesses that can withstand harsh conditions, vibrations, and temperature fluctuations. This durability ensures long-lasting performance and minimizes the risk of breakdowns or malfunctions, leading to increased system uptime and reduced maintenance costs.
Reliability is another key aspect directly influenced by quality. Wiring harnesses serve as the backbone of electrical systems, carrying electrical signals and power throughout. Reliable harnesses ensure uninterrupted signal transmission and power distribution, preventing system failures and ensuring consistent operation. This reliability is especially critical in industries such as automotive, aerospace, and medical devices, where even minor disruptions can have significant consequences.
The commitment to quality by renowned wiring harness manufacturers extends beyond the manufacturing process. It encompasses rigorous testing and inspection procedures to verify the integrity and performance of each harness. By adhering to industry standards and implementing comprehensive quality control measures, these manufacturers deliver products that meet the highest levels of reliability and durability.
In conclusion, the emphasis on quality by renowned wiring harness manufacturers is a testament to their understanding of the critical role these components play in ensuring the performance and safety of electrical systems. By prioritizing durability and reliability, they establish a foundation for successful applications across diverse industries, ranging from automotive and telecommunications to medical devices and industrial machinery.
Customization
In the context of wiring harness manufacturing, customization plays a vital role in catering to the unique demands of diverse industries and applications. Wiring harness manufacturers offer customized solutions that align precisely with specific customer needs and project requirements, ensuring optimal performance and functionality.
- Adaptable Designs: Customization allows manufacturers to modify harness designs to accommodate specific form factors, space constraints, and performance criteria. This adaptability ensures that harnesses seamlessly integrate into complex systems, meeting the exact specifications of the project.
- Tailored Material Selection: Different applications demand specialized materials for wiring harnesses. Customization enables manufacturers to select materials that possess the appropriate electrical properties, temperature resistance, and durability to meet the unique requirements of each project.
- Optimized Functionality: Customization extends to the functional aspects of wiring harnesses. Manufacturers can incorporate additional features, such as shielding, grounding, or specialized connectors, to enhance the functionality and performance of the harness.
- Cost-Effective Solutions: By tailoring harnesses to specific requirements, manufacturers can optimize material usage and production processes, leading to cost-effective solutions without compromising quality.
The ability to offer customized solutions is a key differentiator for wiring harness manufacturers. It empowers them to cater to the diverse needs of industries ranging from automotive and aerospace to medical devices and industrial machinery. By understanding the specific requirements of each project, manufacturers can deliver harnesses that are not only functional but also optimized for performance, safety, and cost-effectiveness.
Expertise
Expertise is a cornerstone of the wiring harness manufacturing industry. Experienced manufacturers possess a comprehensive understanding of harness design, material selection, and manufacturing processes, enabling them to deliver high-quality, customized solutions that meet the unique demands of diverse applications.
- Harness Design Expertise: Seasoned manufacturers have a deep understanding of harness design principles and can optimize harness layout for efficient signal transmission, power distribution, and EMI/RFI mitigation. Their expertise ensures that harnesses are designed to withstand the rigors of the intended environment, including vibrations, temperature fluctuations, and electromagnetic interference.
- Material Selection Expertise: Material selection is critical for harness performance and durability. Experienced manufacturers have in-depth knowledge of the electrical properties, temperature resistance, and mechanical strength of various materials. They can carefully select the most appropriate materials for each application, ensuring optimal performance and longevity.
- Manufacturing Process Expertise: Expertise in manufacturing processes is essential for producing high-quality harnesses. Experienced manufacturers employ advanced manufacturing techniques and equipment to ensure precision, efficiency, and repeatability. Their expertise enables them to optimize production processes, minimize waste, and maintain consistent quality standards.
- Compliance Expertise: Compliance with industry standards and regulations is crucial in the wiring harness manufacturing industry. Experienced manufacturers have a thorough understanding of relevant standards and can design and produce harnesses that meet or exceed these requirements. Their expertise ensures that harnesses are safe, reliable, and compliant with applicable regulations.
The expertise of experienced wiring harness manufacturers is invaluable to industries ranging from automotive and aerospace to medical devices and industrial machinery. By leveraging their knowledge and expertise, manufacturers can deliver customized solutions that enhance system performance, safety, and reliability.
Technology
The integration of advanced technology plays a significant role in the wiring harness manufacturing industry. By employing cutting-edge technology and equipment, manufacturers can achieve higher levels of precision and efficiency in production, leading to enhanced product quality and cost-effectiveness.
- Precision Engineering: Advanced manufacturing technology enables precise cutting, stripping, and crimping of wires, ensuring accurate and consistent connections. This precision is critical for maintaining signal integrity and power distribution throughout the harness.
- Automated Processes: Automation plays a crucial role in efficient production. Automated machines can perform repetitive tasks such as wire cutting, terminal crimping, and harness assembly with speed and accuracy, reducing production time and minimizing human error.
- Quality Control: Advanced technology facilitates rigorous quality control measures. Automated optical inspection (AOI) systems can detect defects and inconsistencies in harnesses, ensuring compliance with industry standards and customer specifications.
- Data Analytics: Manufacturers leverage data analytics to optimize production processes and improve product quality. By analyzing production data, they can identify areas for improvement, reduce waste, and enhance overall efficiency.
The adoption of cutting-edge technology in wiring harness manufacturing transforms the industry by enabling the production of high-quality, reliable harnesses with improved precision, efficiency, and cost-effectiveness. This technological advancement supports the growing demands for complex and customized harnesses in various industries, including automotive, aerospace, and medical devices.
Efficiency
In the competitive landscape of the wiring harness manufacturing industry, efficiency plays a pivotal role in driving success. Streamlined manufacturing processes and optimized designs are crucial elements that enable manufacturers to achieve higher levels of productivity, reduce costs, and meet the growing demands for complex and customized harnesses.
- Lean Manufacturing Techniques: Many wiring harness manufacturers have embraced lean manufacturing principles to optimize their production processes. By eliminating waste and inefficiencies, they can reduce lead times, improve quality, and minimize costs.
- Automated Production Lines: Automation is transforming the wiring harness manufacturing industry. Automated machines can perform repetitive tasks with precision and speed, increasing production efficiency and reducing labor costs.
- Optimized Harness Designs: Experienced manufacturers leverage their expertise to design harnesses that are optimized for ease of assembly and reduced material waste. This contributes to cost savings and improved production efficiency.
- Continuous Improvement: Leading wiring harness manufacturers are committed to continuous improvement. They regularly evaluate their processes and implement innovative solutions to enhance efficiency and productivity.
The focus on efficiency in wiring harness manufacturing not only benefits manufacturers but also their customers. By reducing costs and improving productivity, manufacturers can offer competitive pricing and shorter lead times, ultimately contributing to the success of the industries they serve.
Compliance
Compliance is a critical aspect of the wiring harness manufacturing industry. Reputable manufacturers prioritize adherence to industry standards and regulations to ensure the safety and reliability of their products. This commitment to compliance extends throughout the manufacturing process, from design and material selection to testing and documentation.
Industry standards and regulations serve as guidelines for the design, production, and testing of wiring harnesses. By adhering to these standards, manufacturers can ensure that their products meet or exceed the minimum safety and performance requirements. This is especially important in industries where electrical safety is paramount, such as automotive, aerospace, and medical devices.
Compliance also involves meeting regulatory requirements imposed by government agencies and international organizations. These regulations aim to protect consumers and the environment from electrical hazards and ensure the proper functioning of electrical systems. By complying with these regulations, manufacturers demonstrate their commitment to responsible manufacturing practices and contribute to the overall safety and reliability of electrical products.
The practical significance of compliance for wiring harness manufacturers is multifaceted. Firstly, it helps to ensure the safety of end-users by reducing the risk of electrical accidents and fires. Secondly, compliance can prevent costly legal liabilities and reputational damage that can arise from non-compliant products. Thirdly, it can provide manufacturers with a competitive advantage by demonstrating their commitment to quality and safety.
In conclusion, compliance is a fundamental component of wiring harness manufacturing. By adhering to industry standards and regulations, manufacturers can ensure the safety and reliability of their products, meet regulatory requirements, and gain a competitive advantage in the market.
Creating a Wiring Harness Manufacturer Keyword Chart or Diagram
A wiring harness manufacturer keyword chart or diagram is a useful tool for visualizing the relationships between different keywords and concepts related to the wiring harness manufacturing industry. It can help manufacturers identify and target potential customers, optimize their online presence, and create effective marketing campaigns.
There are many different ways to create a wiring harness manufacturer keyword chart or diagram. Some popular examples include:
- Mind maps: Mind maps are a visual representation of a topic that uses a central concept or keyword and branches out to related subtopics and keywords. They are a great way to brainstorm and organize ideas.
- Flowcharts: Flowcharts are diagrams that show the flow of a process or system. They can be used to map out the steps involved in manufacturing a wiring harness, or to illustrate the relationships between different components of a wiring harness.
- Tables: Tables are a simple way to organize and compare different keywords and concepts. They can be used to list the different types of wiring harnesses, their applications, and their benefits.
The following steps can be used to create a wiring harness manufacturer keyword chart or diagram:
- Start with a central keyword or concept. This could be “wiring harness manufacturer,” “automotive wiring harness,” or “aerospace wiring harness.”
- Brainstorm related keywords and concepts. Think about the different types of wiring harnesses, their applications, their benefits, and their target customers.
- Organize your keywords and concepts. Use a mind map, flowchart, or table to organize your keywords and concepts in a logical way.
- Add additional information. Include additional information about each keyword or concept, such as its definition, its importance, or its relationship to other keywords or concepts.
- Review and revise. Once you have created a draft of your keyword chart or diagram, review it carefully and make any necessary revisions.
Wiring harness manufacturer keyword charts or diagrams can be a valuable tool for manufacturers in the wiring harness industry. By following the steps outlined above, manufacturers can create a visual representation of their target keywords and concepts, which can help them to develop more effective marketing campaigns and reach their target audience.
FAQs on Wiring Harness Manufacturing
Frequently asked questions and their respective answers concerning the field of wiring harness manufacturing are addressed below.
Question 1: What factors should be considered when selecting a wiring harness manufacturer?
Answer: Choosing a wiring harness manufacturer requires careful evaluation of various factors, including their experience, quality standards, certifications, customer service, and ability to meet specific requirements and industry regulations.
Question 2: What are the different types of wiring harnesses?
Answer: Wiring harnesses vary based on their applications and can be classified into automotive harnesses, industrial harnesses, aerospace harnesses, medical harnesses, and custom harnesses designed for specific purposes.
Question 3: How can I ensure the quality and reliability of a wiring harness?
Answer: To guarantee quality and reliability, look for manufacturers who adhere to industry standards, conduct thorough testing, and provide documentation to demonstrate their commitment to excellence in production.
Question 4: What are the benefits of using custom wiring harnesses?
Answer: Custom wiring harnesses offer tailored solutions that meet specific requirements, resulting in improved performance, reduced assembly time, enhanced reliability, and cost optimization.
Question 5: What is the importance of proper wiring harness design?
Answer: Proper wiring harness design is crucial as it determines the functionality, durability, safety, and ease of installation, ultimately affecting the overall performance and lifespan of the electrical system.
Question 6: What are the industry trends and advancements in wiring harness manufacturing?
Answer: The wiring harness manufacturing industry is constantly evolving, with advancements in materials, automation, and design software, leading to improved efficiency, cost-effectiveness, and innovation.
By understanding these key aspects of wiring harness manufacturing, individuals can make informed decisions, select reliable suppliers, and leverage the benefits of custom solutions to meet their specific requirements.
Transitioning to the next article section: Wiring Harness Manufacturing: A Comprehensive Overview.
Conclusion
The exploration of wiring harness manufacturing in this article has shed light on the critical role these components play in diverse industries, ranging from automotive and aerospace to telecommunications and medical devices. The expertise, precision, and commitment to quality exhibited by reputable manufacturers ensure the reliable functioning of electrical systems, enhancing performance, safety, and efficiency.
As technology continues to advance and industries evolve, the demand for customized and high-quality wiring harnesses will only increase. By embracing innovation and leveraging the latest advancements in materials, automation, and design software, wiring harness manufacturers can remain at the forefront of this dynamic industry. Their unwavering commitment to excellence will continue to drive progress and empower industries to harness the full potential of electrical systems.
Youtube Video:
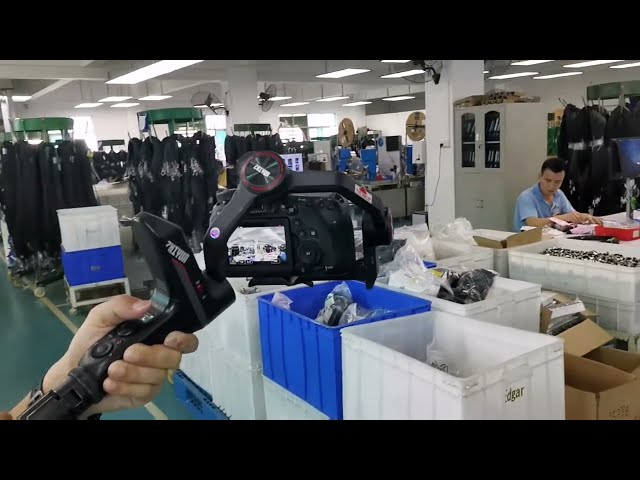