Single pulse encoder wiring is a specialized electrical wiring technique used to connect a single pulse encoder to a control system. A single pulse encoder is a type of rotary encoder that generates one electrical pulse for each mechanical revolution of its shaft. This type of encoder is often used in industrial applications to measure speed, position, or direction of rotating machinery.
The wiring of a single pulse encoder is relatively simple and straightforward. The encoder typically has three wires: a power wire, a ground wire, and a signal wire. The power wire is connected to a power supply, the ground wire is connected to a ground reference, and the signal wire is connected to an input on the control system.
Single pulse encoder wiring is an important part of many industrial control systems. It allows for accurate and reliable measurement of speed, position, and direction of rotating machinery. This information can be used for a variety of purposes, such as controlling the speed of a motor, positioning a robotic arm, or tracking the movement of a conveyor belt.
Single Pulse Encoder Wiring
Single pulse encoder wiring is a critical component of many industrial control systems. It allows for accurate and reliable measurement of speed, position, and direction of rotating machinery. This information can be used for a variety of purposes, such as controlling the speed of a motor, positioning a robotic arm, or tracking the movement of a conveyor belt.
- Electrical Wiring Technique
- Connects Encoder to Control System
- Measures Speed, Position, Direction
- Three Wires: Power, Ground, Signal
- Simple and Straightforward Wiring
- Industrial Control Systems
These key aspects highlight the importance of single pulse encoder wiring in industrial control systems. By understanding these aspects, engineers can ensure that their wiring isand that their control systems are operating at peak efficiency.
Electrical Wiring Technique
Electrical wiring technique is the foundation of single pulse encoder wiring. It involves the proper connection of electrical wires to a single pulse encoder and a control system. The electrical wiring technique ensures that the encoder can accurately and reliably transmit data to the control system.
The electrical wiring technique for a single pulse encoder typically involves three wires: a power wire, a ground wire, and a signal wire. The power wire is connected to a power supply, the ground wire is connected to a ground reference, and the signal wire is connected to an input on the control system.
The electrical wiring technique must be performed carefully and precisely to ensure that the encoder is functioning properly. Incorrect wiring can lead to inaccurate data transmission or even damage to the encoder or the control system.
Understanding the electrical wiring technique for single pulse encoders is essential for engineers and technicians who work with industrial control systems. By understanding the proper wiring technique, they can ensure that their systems are operating at peak efficiency and that they are able to accurately and reliably measure speed, position, and direction of rotating machinery.
Connects Encoder to Control System
In the context of single pulse encoder wiring, the connection between the encoder and the control system is crucial for accurate and reliable data transmission. This connection allows the encoder to send information about speed, position, and direction of rotating machinery to the control system, which can then use this information to make decisions and control the machinery accordingly.
-
Electrical Signals
The connection between the encoder and the control system is established through electrical signals. The encoder generates electrical pulses that are sent to the control system through wires. The control system then interprets these pulses to determine the speed, position, and direction of the rotating machinery.
-
Communication Protocols
The encoder and the control system must use the same communication protocol in order to communicate effectively. The communication protocol defines the format of the electrical signals and the rules for how the encoder and the control system exchange data.
-
Wiring Standards
The wiring between the encoder and the control system must be installed according to specific wiring standards. These standards ensure that the wiring is safe and reliable, and that the encoder and the control system can communicate effectively.
-
Troubleshooting
If the encoder is not communicating properly with the control system, it is important to troubleshoot the wiring. This may involve checking the electrical connections, the communication protocol, and the wiring standards.
By understanding the connection between the encoder and the control system, engineers and technicians can ensure that their systems are operating at peak efficiency and that they are able to accurately and reliably measure speed, position, and direction of rotating machinery.
Measures Speed, Position, Direction
Single pulse encoder wiring is a critical component of industrial control systems that measure speed, position, and direction of rotating machinery. This information is essential for a wide range of applications, such as controlling the speed of a motor, positioning a robotic arm, or tracking the movement of a conveyor belt.
The ability to measure speed, position, and direction is made possible by the electrical pulses generated by the single pulse encoder. These pulses are sent to the control system through wires, where they are interpreted to determine the speed, position, and direction of the rotating machinery.
The accuracy and reliability of the speed, position, and direction measurements depend on the quality of the single pulse encoder wiring. Poor wiring can lead to inaccurate data transmission or even damage to the encoder or the control system.
Three Wires
In single pulse encoder wiring, the three wirespower, ground, and signalplay a crucial role in ensuring accurate and reliable data transmission. Each wire has a specific function and must be properly connected to the encoder and the control system.
The power wire supplies electricity to the encoder, enabling it to generate electrical pulses. The ground wire provides a reference point for the electrical signals, ensuring that the encoder and the control system are operating at the same electrical potential. The signal wire carries the electrical pulses generated by the encoder to the control system, where they are interpreted to determine the speed, position, and direction of the rotating machinery.
The importance of these three wires cannot be overstated. Without the power wire, the encoder would not be able to generate electrical pulses. Without the ground wire, the electrical signals would be unreliable and inaccurate. And without the signal wire, the control system would not be able to receive the data from the encoder.
Understanding the connection between these three wires and single pulse encoder wiring is essential for engineers and technicians who work with industrial control systems. By understanding the function of each wire and the importance of proper wiring, they can ensure that their systems are operating at peak efficiency and that they are able to accurately and reliably measure speed, position, and direction of rotating machinery.
Simple and Straightforward Wiring
In the realm of industrial control systems, single pulse encoder wiring stands out for its simplicity and straightforwardness. This characteristic plays a vital role in ensuring the accuracy and reliability of these systems, which are essential for a wide range of applications.
The simplicity of single pulse encoder wiring lies in its use of only three wires: power, ground, and signal. This minimal configuration reduces the risk of wiring errors and makes installation and maintenance tasks less complex. Furthermore, the straightforward nature of the wiring allows for easy troubleshooting, minimizing downtime and maximizing system efficiency.
The importance of simple and straightforward wiring in single pulse encoder wiring cannot be overstated. It contributes directly to the accuracy and reliability of the data transmission between the encoder and the control system. This accurate data is crucial for controlling the speed, position, and direction of rotating machinery with precision.
In conclusion, the simplicity and straightforwardness of single pulse encoder wiring is not merely a convenience but a critical factor in ensuring the effectiveness of industrial control systems. By understanding the significance of this characteristic, engineers and technicians can optimize the performance of their systems and achieve greater efficiency and accuracy in their operations.
Industrial Control Systems
Within the domain of industrial automation, single pulse encoder wiring plays a pivotal role in the operation of industrial control systems (ICSs). These systems serve as the backbone of modern industrial processes, enabling precise control over machinery, equipment, and entire production lines.
-
Components of ICSs
ICSs comprise a network of interconnected components, including programmable logic controllers (PLCs), distributed control systems (DCSs), and supervisory control and data acquisition (SCADA) systems. These components communicate with each other and with field devices, such as sensors and actuators, to monitor and control industrial processes in real time.
-
Single Pulse Encoder Wiring in ICSs
Single pulse encoder wiring is a critical aspect of ICSs, as it provides the means to connect single pulse encoders to the control system. Single pulse encoders are electromechanical devices that convert mechanical motion into electrical pulses, providing precise information about the speed, position, and direction of rotating machinery.
-
Role of Single Pulse Encoders
Single pulse encoders are used in a wide range of industrial applications, such as robotics, automated assembly lines, and process control. Their ability to provide accurate and reliable data on the motion of rotating machinery is essential for precise control and monitoring.
-
Implications for ICSs
Proper single pulse encoder wiring is crucial for the accuracy and reliability of ICSs. Incorrect wiring can lead to erroneous data, which can compromise the performance and safety of the entire system. Therefore, it is essential for engineers and technicians to have a thorough understanding of single pulse encoder wiring practices.
In conclusion, single pulse encoder wiring is an integral part of industrial control systems, providing a means to connect single pulse encoders and enabling precise control over industrial processes. Understanding the components, role, and implications of single pulse encoder wiring is essential for ensuring the accuracy and reliability of these systems.
Single Pulse Encoder Wiring Diagrams and Guidelines
Single pulse encoder wiring diagrams and guidelines are essential for ensuring the accurate and reliable operation of industrial control systems. These diagrams and guidelines provide a visual representation of the electrical connections between a single pulse encoder and a control system, and they specify the steps necessary to create these connections.
There are a number of different types of single pulse encoder wiring diagrams and guidelines available. Some of the most common include:
- Basic single pulse encoder wiring diagrams: These diagrams show the basic electrical connections between a single pulse encoder and a control system. They typically include a schematic diagram of the encoder, a wiring diagram, and a table of connection points.
- Advanced single pulse encoder wiring diagrams: These diagrams provide more detailed information about the electrical connections between a single pulse encoder and a control system. They may include information about the type of encoder, the type of control system, and the specific wiring requirements for the application.
- Single pulse encoder wiring guidelines: These guidelines provide step-by-step instructions on how to wire a single pulse encoder to a control system. They typically include information about the tools and materials needed, the safety precautions to take, and the specific steps to follow.
When creating a single pulse encoder wiring diagram or guideline, it is important to follow the manufacturer’s instructions carefully. These instructions will provide the specific information needed to ensure that the encoder is wired correctly and that the control system is able to receive the data from the encoder.
In conclusion, single pulse encoder wiring diagrams and guidelines are essential for ensuring the accurate and reliable operation of industrial control systems. By following the manufacturer’s instructions carefully, engineers and technicians can create wiring diagrams and guidelines that will help to ensure that their systems are operating at peak efficiency.
Frequently Asked Questions about Single Pulse Encoder Wiring
Single pulse encoder wiring is a critical aspect of industrial control systems, enabling accurate and reliable measurement of speed, position, and direction of rotating machinery. Here are some frequently asked questions about single pulse encoder wiring:
Question 1: What is the purpose of single pulse encoder wiring?
Single pulse encoder wiring connects a single pulse encoder to a control system, allowing the encoder to transmit data about speed, position, and direction of rotating machinery to the control system.
Question 2: What are the different types of single pulse encoder wiring diagrams?
There are three main types of single pulse encoder wiring diagrams: basic, advanced, and guidelines. Basic diagrams show the basic electrical connections, advanced diagrams provide more detailed information, and guidelines provide step-by-step instructions.
Question 3: How do I create a single pulse encoder wiring diagram?
To create a single pulse encoder wiring diagram, follow the manufacturer’s instructions carefully. These instructions will provide the specific information needed to ensure that the encoder is wired correctly and that the control system is able to receive the data from the encoder.
Question 4: What are some common mistakes to avoid when wiring a single pulse encoder?
Common mistakes to avoid when wiring a single pulse encoder include using the wrong type of wire, connecting the wires incorrectly, and not following the manufacturer’s instructions.
Question 5: What are the benefits of using single pulse encoder wiring?
The benefits of using single pulse encoder wiring include accurate and reliable data transmission, ease of installation and maintenance, and cost-effectiveness.
Question 6: Where can I find more information about single pulse encoder wiring?
More information about single pulse encoder wiring can be found in the manufacturer’s documentation, industry publications, and online resources.
In conclusion, single pulse encoder wiring is a critical aspect of industrial control systems, enabling accurate and reliable measurement of speed, position, and direction of rotating machinery. By understanding the purpose, types, and benefits of single pulse encoder wiring, engineers and technicians can ensure that their systems are operating at peak efficiency.
Transition to the next article section: Single Pulse Encoder Wiring Best Practices
Conclusion
Single pulse encoder wiring is a critical aspect of industrial control systems, enabling accurate and reliable measurement of speed, position, and direction of rotating machinery. This article has explored the purpose, types, benefits, and best practices of single pulse encoder wiring, providing engineers and technicians with the knowledge necessary to ensure that their systems are operating at peak efficiency.
As industrial automation continues to advance, the demand for accurate and reliable data transmission will only increase. Single pulse encoder wiring will continue to play a vital role in meeting this demand, providing a cost-effective and reliable solution for connecting single pulse encoders to control systems.
Youtube Video:
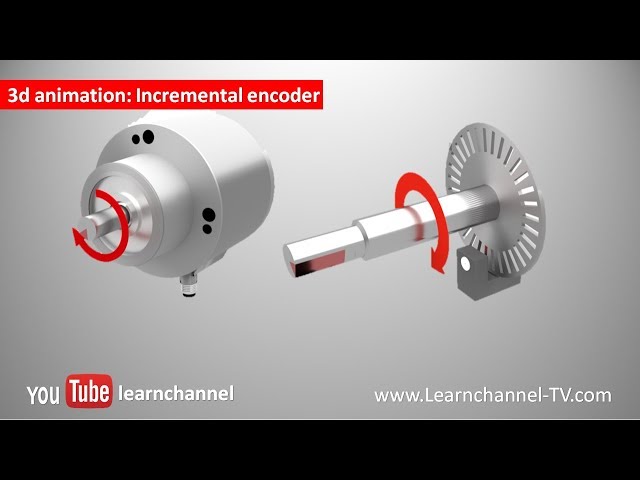