A wiring harness is a system of wires that connects electrical components in a vehicle, aircraft, or other machine. Checking your wiring harness is an important part of preventive maintenance, as it can help you identify and fix problems before they cause major issues.
There are a few different ways to check your wiring harness. One way is to use a multimeter to test for continuity. To do this, simply connect the multimeter to the two ends of the wire you want to test. If the multimeter beeps, then the wire is continuous. If it doesn’t beep, then the wire is broken or damaged.
Another way to check your wiring harness is to look for any signs of damage. This could include cuts, nicks, or burns in the insulation. If you find any damage, you should repair or replace the wire immediately.
Checking your wiring harness is a simple but important task that can help you keep your vehicle or machine running smoothly. By following these steps, you can ensure that your wiring harness is in good condition and that your electrical system is functioning properly.
How to Check Your Wiring Harness
A wiring harness is a system of wires that connects electrical components in a vehicle, aircraft, or other machine. Checking your wiring harness is an important part of preventive maintenance, as it can help you identify and fix problems before they cause major issues.
- Visual Inspection: Look for any signs of damage, such as cuts, nicks, or burns in the insulation.
- Continuity Test: Use a multimeter to test for continuity between the two ends of each wire.
- Voltage Drop Test: Measure the voltage drop across each wire to identify any potential problems.
- Insulation Resistance Test: Test the insulation resistance of each wire to ensure that it is not damaged.
- Ground Fault Test: Test for any ground faults in the wiring harness.
- Circuit Analysis: Analyze the circuit diagram to identify any potential trouble spots.
- Diagnostic Tools: Use diagnostic tools, such as a scan tool or oscilloscope, to help identify problems.
By following these steps, you can ensure that your wiring harness is in good condition and that your electrical system is functioning properly. This can help you avoid costly repairs and keep your vehicle or machine running smoothly.
Visual Inspection
Visual inspection is an important part of checking your wiring harness, as it can help you identify potential problems early on. By looking for any signs of damage, such as cuts, nicks, or burns in the insulation, you can take steps to repair or replace the damaged wire before it causes a more serious issue.
- Identifying Potential Problems: Visual inspection can help you identify potential problems with your wiring harness before they cause major issues. For example, if you see any cuts or nicks in the insulation, this could be a sign that the wire has been damaged and is at risk of breaking. Similarly, if you see any burns in the insulation, this could be a sign that the wire has been overloaded and is at risk of overheating.
- Preventing Electrical Fires: By identifying and repairing damaged wires, you can help to prevent electrical fires. Electrical fires can be caused by a variety of factors, including damaged wiring. By taking the time to visually inspect your wiring harness and repair any damaged wires, you can help to reduce the risk of an electrical fire.
- Maintaining Electrical System Functionality: A well-maintained wiring harness is essential for the proper functioning of your electrical system. By visually inspecting your wiring harness and repairing any damaged wires, you can help to ensure that your electrical system is functioning properly and that all of your electrical components are receiving the power they need.
Visual inspection is a simple but effective way to check your wiring harness and identify potential problems. By following these steps, you can help to keep your electrical system running smoothly and avoid costly repairs.
Continuity Test
A continuity test is an essential part of checking your wiring harness, as it can help you identify broken or damaged wires. A multimeter is a simple tool that can be used to perform a continuity test. To do this, simply connect the multimeter to the two ends of the wire you want to test. If the multimeter beeps, then the wire is continuous. If it doesn’t beep, then the wire is broken or damaged.
Continuity testing is important because it can help you identify potential problems with your wiring harness before they cause major issues. For example, if you find a broken wire, you can repair or replace it before it causes an electrical short or other problems. Continuity testing can also help you identify intermittent problems, which can be difficult to diagnose. By regularly performing continuity tests on your wiring harness, you can help to ensure that your electrical system is functioning properly and that all of your electrical components are receiving the power they need.
Here are some examples of how continuity testing can be used to check your wiring harness:
- Identifying Broken Wires: Continuity testing can be used to identify broken wires by measuring the resistance between the two ends of the wire. If the resistance is infinite, then the wire is broken.
- Identifying Damaged Wires: Continuity testing can also be used to identify damaged wires by measuring the insulation resistance between the wire and the ground. If the insulation resistance is low, then the wire is damaged.
- Identifying Intermittent Problems: Continuity testing can be used to identify intermittent problems by wiggling the wire while measuring the continuity. If the continuity is intermittent, then the wire may have a loose connection or other problem.
By understanding the connection between continuity testing and checking your wiring harness, you can help to ensure that your electrical system is functioning properly and that all of your electrical components are receiving the power they need.
Voltage Drop Test
A voltage drop test is an important part of checking your wiring harness, as it can help you identify potential problems with your electrical system. A voltage drop occurs when there is a resistance to the flow of electricity in a wire. This can be caused by a variety of factors, including loose connections, damaged wires, or overloaded circuits.
By measuring the voltage drop across each wire, you can identify areas where there is excessive resistance. This can help you to identify and fix problems before they cause more serious issues, such as electrical fires or equipment damage.
To perform a voltage drop test, you will need a voltmeter. Connect the voltmeter to the positive and negative terminals of the battery. Then, measure the voltage drop across each wire in the harness. The voltage drop should be less than 5% of the battery voltage. If the voltage drop is greater than 5%, then there is excessive resistance in the wire.
Voltage drop testing is a simple but effective way to check your wiring harness and identify potential problems. By following these steps, you can help to ensure that your electrical system is functioning properly and that all of your electrical components are receiving the power they need.
Insulation Resistance Test
An insulation resistance test is an important part of checking your wiring harness, as it can help you identify potential problems with the insulation of your wires. The insulation of your wires is what protects them from short circuits and other electrical hazards. If the insulation is damaged, it can lead to a variety of problems, including electrical fires.
- Identifying Damaged Insulation: An insulation resistance test can help you identify damaged insulation by measuring the resistance between the wire and the ground. If the resistance is low, then the insulation is damaged.
- Preventing Electrical Fires: By identifying and repairing damaged insulation, you can help to prevent electrical fires. Electrical fires can be caused by a variety of factors, including damaged insulation. By taking the time to test the insulation resistance of your wires and repair any damaged insulation, you can help to reduce the risk of an electrical fire.
- Maintaining Electrical System Functionality: A well-maintained wiring harness is essential for the proper functioning of your electrical system. By testing the insulation resistance of your wires and repairing any damaged insulation, you can help to ensure that your electrical system is functioning properly and that all of your electrical components are receiving the power they need.
Insulation resistance testing is a simple but effective way to check your wiring harness and identify potential problems. By following these steps, you can help to keep your electrical system running smoothly and avoid costly repairs.
Ground Fault Test
A ground fault test is an important part of checking your wiring harness, as it can help you identify potential problems with the grounding of your electrical system. A ground fault occurs when there is an unintended path for electricity to flow to the ground. This can be caused by a variety of factors, including damaged insulation, loose connections, or faulty equipment.
- Identifying Ground Faults: A ground fault test can help you identify ground faults by measuring the resistance between the ground and the electrical system. If the resistance is low, then there is a ground fault.
- Preventing Electrical Fires: By identifying and repairing ground faults, you can help to prevent electrical fires. Electrical fires can be caused by a variety of factors, including ground faults. By taking the time to test for ground faults and repair any problems, you can help to reduce the risk of an electrical fire.
- Maintaining Electrical System Functionality: A well-maintained wiring harness is essential for the proper functioning of your electrical system. By testing for ground faults and repairing any problems, you can help to ensure that your electrical system is functioning properly and that all of your electrical components are receiving the power they need.
Ground fault testing is a simple but effective way to check your wiring harness and identify potential problems. By following these steps, you can help to keep your electrical system running smoothly and avoid costly repairs.
Circuit Analysis
Circuit analysis is an important part of checking your wiring harness, as it can help you identify potential problems with your electrical system before they cause major issues. A circuit diagram is a schematic representation of your electrical system, showing the connections between the different components. By analyzing the circuit diagram, you can identify potential trouble spots, such as overloaded circuits or loose connections.
For example, if you are experiencing electrical problems, such as flickering lights or blown fuses, you can use a circuit diagram to trace the circuit and identify the source of the problem. Once you have identified the source of the problem, you can take steps to repair it and prevent it from happening again.
Circuit analysis is a valuable tool for checking your wiring harness and ensuring that your electrical system is functioning properly. By taking the time to analyze the circuit diagram and identify potential trouble spots, you can help to prevent electrical problems and keep your electrical system running smoothly.
Diagnostic Tools
Diagnostic tools, such as scan tools and oscilloscopes, are essential for checking your wiring harness and identifying problems. These tools allow you to test the electrical signals in your wiring harness and identify any faults or problems. For example, a scan tool can be used to read the diagnostic trouble codes (DTCs) from your vehicle’s computer. These codes can help you identify the source of a problem, such as a faulty sensor or a loose connection.
Oscilloscopes can be used to measure the voltage and frequency of electrical signals in your wiring harness. This information can be used to identify problems such as shorts, opens, and intermittent connections. By using diagnostic tools, you can quickly and easily identify problems with your wiring harness and take steps to repair them.
Diagnostic tools are an essential part of checking your wiring harness and ensuring that your electrical system is functioning properly. By using these tools, you can identify problems early on and prevent them from causing major issues. This can save you time and money in the long run.
How to Create a Wiring Harness Inspection Chart or Diagram
A wiring harness inspection chart or diagram is a valuable tool for checking your wiring harness and ensuring that your electrical system is functioning properly. By following the steps below, you can create a chart or diagram that will help you to identify potential problems with your wiring harness early on and prevent them from causing major issues.
Steps to Create a Wiring Harness Inspection Chart or Diagram:
- Gather your materials. You will need a piece of paper, a pencil, and a ruler. You may also want to use a computer-aided design (CAD) program to create your chart or diagram.
- Draw a diagram of your wiring harness. The diagram should show the layout of the wiring harness, including the location of all of the wires, connectors, and components. Be sure to label each wire and component clearly.
-
Create a table to list the inspection points. The table should include the following columns:
- Wire Number
- Connector Number
- Component
- Inspection Point
- Inspection Method
- Acceptance Criteria
- Fill in the table. For each inspection point, specify the wire number, connector number, component, inspection point, inspection method, and acceptance criteria. The acceptance criteria should be based on the manufacturer’s specifications for the wiring harness.
- Review the chart or diagram. Once you have completed the chart or diagram, review it carefully to ensure that it is accurate and complete.
Examples of Wiring Harness Inspection Charts and Diagrams:
- Wiring Harness Inspection Chart: This type of chart is a simple table that lists the inspection points for a wiring harness. It is typically used for simple wiring harnesses with a limited number of wires and components.
- Wiring Harness Inspection Diagram: This type of diagram is a more detailed representation of a wiring harness. It shows the layout of the wiring harness, including the location of all of the wires, connectors, and components. It is typically used for complex wiring harnesses with a large number of wires and components.
Conclusion:
By following the steps above, you can create a wiring harness inspection chart or diagram that will help you to check your wiring harness and ensure that your electrical system is functioning properly. This can save you time and money in the long run by preventing electrical problems and keeping your electrical system running smoothly.
Frequently Asked Questions about Wiring Harness Inspection
Wiring harnesses are essential components of electrical systems, and regular inspection is crucial for maintaining their integrity and functionality. Here are answers to some frequently asked questions about checking wiring harnesses:
Question 1: Why is it important to check wiring harnesses regularly?
Regular inspection of wiring harnesses helps identify potential issues early on, preventing minor problems from escalating into major electrical faults. It ensures the reliability and safety of electrical systems, minimizing downtime and costly repairs.
Question 2: What are some signs that indicate a wiring harness needs inspection?
Indicators of potential wiring harness issues include visible damage such as cuts, abrasions, or burns on the insulation; loose or disconnected connectors; and signs of corrosion or oxidation on terminals or wires.
Question 3: What are the different methods for checking wiring harnesses?
There are several methods for checking wiring harnesses, including visual inspection, continuity testing with a multimeter, insulation resistance testing, voltage drop testing, and ground fault testing. Each method serves a specific purpose in identifying different types of faults.
Question 4: What tools are needed to check wiring harnesses?
Basic tools required for wiring harness inspection include a flashlight, magnifying glass, multimeter, and insulation tester. More advanced tools like oscilloscopes and scan tools may be necessary for in-depth analysis and fault diagnosis.
Question 5: How often should wiring harnesses be inspected?
The frequency of wiring harness inspection depends on the operating environment, usage patterns, and criticality of the system. As a general rule, it’s recommended to inspect wiring harnesses annually or more frequently in harsh or demanding conditions.
Question 6: What are the consequences of neglecting wiring harness inspection?
Neglecting wiring harness inspection can lead to undetected faults, increasing the risk of electrical failures, fires, or system malfunctions. It can also compromise the safety and reliability of electrical equipment and systems.
Summary:
Regular inspection of wiring harnesses is crucial for maintaining the integrity and functionality of electrical systems. By identifying potential issues early on, costly repairs and downtime can be prevented. Proper inspection techniques and tools are essential to ensure the reliability and safety of electrical systems.
Next Article Section: Advanced Wiring Harness Inspection Techniques
Conclusion
Regular inspection of wiring harnesses is a crucial aspect of maintaining the integrity and functionality of electrical systems. By understanding the importance of checking wiring harnesses, employing the appropriate inspection methods, and utilizing the necessary tools, individuals can proactively identify and address potential issues before they escalate into major electrical faults.
Neglecting wiring harness inspection can compromise the safety and reliability of electrical equipment and systems, potentially leading to costly repairs, downtime, and even electrical hazards. Therefore, it is essential to incorporate regular wiring harness inspection into maintenance routines to ensure the smooth operation and longevity of electrical systems.
Youtube Video:
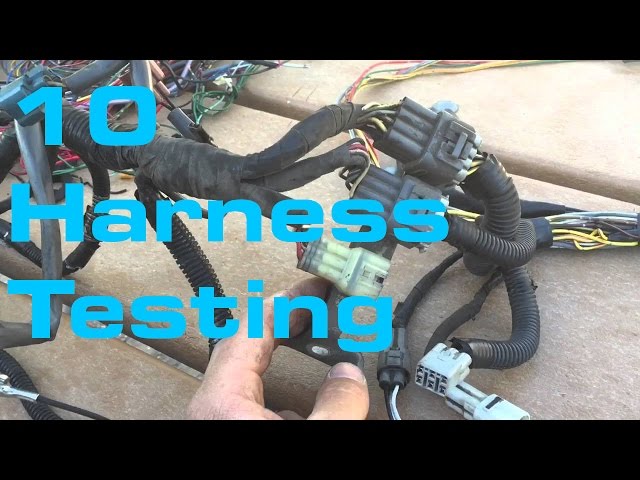