Cloth wrapped insulated electrical wiring refers to the type of electrical wiring that has an insulating layer of cloth wrapped around the conducting wires. This type of wiring was commonly used in the early days of electrical installations, but has since been replaced by more modern and safer materials such as PVC or rubber.
Cloth wrapped insulated electrical wiring was important because it provided a degree of protection against electrical shocks and fires. The cloth served as a barrier between the live wires and any exposed surfaces, reducing the risk of accidental contact. Additionally, the cloth wrapping helped to prevent the wires from overheating, which could lead to electrical fires.
However, cloth wrapped insulated electrical wiring also had some drawbacks. The cloth was susceptible to moisture and could become damaged over time, which could compromise the safety of the wiring. Additionally, the cloth wrapping was not very flexible, making it difficult to install in tight spaces. As a result, cloth wrapped insulated electrical wiring has been largely replaced by more modern materials that offer better performance and safety.
Cloth Wrapped Insulated Electrical Wiring
Cloth wrapped insulated electrical wiring played a crucial role in the development of electrical systems, providing insulation and protection against electrical hazards. Its key aspects include:
- Insulating Material: Cloth served as an insulating layer, preventing electrical current from escaping and causing shocks.
- Fire Resistance: The cloth wrapping provided some degree of fire resistance, reducing the risk of electrical fires.
- Flexibility: Despite its cloth covering, this wiring offered flexibility for installation in various spaces.
- Durability: The cloth wrapping protected the wires from physical damage and environmental factors.
- Historical Significance: Cloth wrapped insulated electrical wiring was widely used in early electrical installations.
- Safety Concerns: Over time, the cloth insulation could deteriorate, posing safety hazards.
- Modern Replacements: Advanced materials like PVC and rubber have replaced cloth in electrical wiring due to improved insulation and safety.
These aspects highlight the significance of cloth wrapped insulated electrical wiring in the evolution of electrical systems. While it provided insulation and protection in the early days, modern materials offer enhanced safety and performance, ensuring the safe and efficient distribution of electricity.
Insulating Material
In the context of cloth wrapped insulated electrical wiring, the insulating material plays a critical role in preventing electrical accidents and ensuring the safe operation of electrical systems. The cloth serves as a non-conductive barrier, preventing the flow of electrical current from the live wires to the surroundings. This insulating layer effectively minimizes the risk of electrical shocks and short circuits, which could lead to fires or other hazards.
The use of cloth as an insulating material in electrical wiring was a significant advancement in electrical safety. Before the advent of cloth insulation, electrical wires were often bare or covered with materials that provided minimal protection against electrical hazards. The introduction of cloth wrapping as an insulating layer greatly reduced the incidence of electrical accidents and paved the way for the widespread adoption of electricity in homes, industries, and public spaces.
Even today, cloth wrapped insulated electrical wiring can still be found in some older buildings and historical structures. While modern materials such as PVC and rubber have largely replaced cloth as the insulating material of choice, the understanding of the insulating properties of cloth remains an important concept in electrical engineering and safety practices. It serves as a reminder of the importance of proper insulation in preventing electrical hazards and ensuring the safe and efficient distribution of electricity.
Fire Resistance
The fire-resistant properties of cloth wrapped insulated electrical wiring played a significant role in enhancing electrical safety, particularly in the early days of electrical installations. The cloth wrapping served as a protective layer, reducing the risk of electrical fires caused by overheating or insulation failure.
- Prevention of Fire Spread: The cloth wrapping acted as a barrier, preventing flames from easily spreading along the wires. This was especially important in situations where wires were bundled together or installed in close proximity to combustible materials.
- Containment of Electrical Arcs: In the event of an electrical arc or fault, the cloth wrapping helped to contain the arc and prevent it from igniting surrounding materials. The non-flammable nature of the cloth wrapping reduced the risk of fire propagation.
- Delaying Ignition: Even if the cloth wrapping eventually ignited, it provided valuable time for occupants to evacuate and firefighters to respond. The slow-burning characteristics of the cloth wrapping allowed for early detection and intervention, minimizing the potential damage caused by the fire.
While modern materials such as PVC and rubber offer superior fire resistance compared to cloth, the understanding of fire safety principles remains essential in electrical wiring practices. The use of fire-resistant materials and proper installation techniques helps to prevent electrical fires and ensures the safety of buildings and occupants.
Flexibility
The flexibility of cloth wrapped insulated electrical wiring was a significant advantage in the early days of electrical installations. Unlike rigid metal conduits or armored cables, cloth wrapped wiring could be easily bent and shaped to fit into tight spaces and around obstacles. This flexibility made it ideal for use in homes, businesses, and industrial settings, where wires needed to be routed through walls, ceilings, and other tight spaces.
The flexibility of cloth wrapped insulated electrical wiring can be attributed to several factors:
- Thin and pliable cloth: The cloth wrapping was typically made of thin, tightly woven cotton or linen, which allowed it to bend and conform to different shapes without losing its insulating properties.
- Multiple small conductors: Cloth wrapped insulated electrical wiring often consisted of multiple small conductors twisted together, rather than a single large conductor. This construction made the wiring more flexible and easier to handle.
- Lack of a protective sheath: Unlike modern electrical cables, which have a protective outer sheath, cloth wrapped insulated electrical wiring did not have a rigid outer covering. This allowed the wiring to be bent and shaped more easily.
The flexibility of cloth wrapped insulated electrical wiring made it a versatile and adaptable solution for a wide range of electrical installations. It could be used in both residential and commercial buildings, and it was particularly well-suited for use in tight spaces or where wires needed to be routed around obstacles.
Durability
The durability of cloth wrapped insulated electrical wiring was a key factor in its widespread adoption and use in early electrical installations. The cloth wrapping provided a protective layer that shielded the wires from various physical and environmental hazards, ensuring their longevity and reliable performance.
The cloth wrapping protected the wires from:
- Abrasion and wear: The cloth wrapping acted as a buffer, preventing the wires from being damaged by rubbing against other surfaces or objects. This was especially important in areas where the wires were exposed to movement or vibration.
- Moisture and humidity: The cloth wrapping provided a degree of moisture resistance, protecting the wires from corrosion and electrical faults caused by exposure to humidity or water. This was particularly important in damp or humid environments, such as basements, bathrooms, and outdoor locations.
- Heat and cold: The cloth wrapping helped to insulate the wires, protecting them from extreme temperatures. This prevented the wires from overheating or becoming brittle in cold conditions, ensuring their continued functionality.
The durability of cloth wrapped insulated electrical wiring made it a reliable and long-lasting solution for a wide range of electrical applications. It could withstand the rigors of daily use and exposure to various environmental conditions, ensuring the safe and efficient distribution of electricity.
Historical Significance
Cloth wrapped insulated electrical wiring played a significant role in the development and widespread adoption of electrical systems. Its historical significance is intertwined with the following aspects:
- Early Electrical Infrastructure: Cloth wrapped insulated electrical wiring was a key component in the establishment of early electrical infrastructure. It was used in the first electrical grids, power plants, and electrical distribution systems.
- Residential and Commercial Electrification: The use of cloth wrapped insulated electrical wiring enabled the electrification of homes, businesses, and public spaces. It allowed for the installation of lighting, appliances, and other electrical devices, transforming daily life.
- Industrial Applications: Cloth wrapped insulated electrical wiring was essential for the development of industries and factories. It provided the electrical power needed to operate machinery, tools, and production lines.
- Safety and Reliability: In its time, cloth wrapped insulated electrical wiring represented a significant improvement in electrical safety. It reduced the risk of electrical shocks, fires, and other hazards.
The historical significance of cloth wrapped insulated electrical wiring lies in its pioneering role in shaping the electrical infrastructure and enabling the widespread use of electricity. While modern materials have replaced cloth in electrical wiring, understanding its historical significance provides valuable insights into the evolution of electrical systems and the advancements that have led to our present-day electrical infrastructure.
Safety Concerns
The safety concerns associated with cloth wrapped insulated electrical wiring stem from the potential deterioration of the cloth insulation over time. As the wiring ages, the cloth insulation can become frayed, cracked, or damaged, compromising its ability to provide adequate protection against electrical hazards.
Deteriorated cloth insulation can lead to several safety hazards, including:
- Electrical shocks: Damaged insulation can expose live wires, increasing the risk of electrical shocks to anyone who comes into contact with them.
- Electrical fires: Deteriorated insulation can also lead to electrical fires, as exposed wires can come into contact with flammable materials and ignite them.
- Short circuits: Damaged insulation can create a path for electrical current to flow unintentionally, causing short circuits that can damage electrical equipment or even start fires.
The importance of recognizing and addressing safety concerns related to cloth wrapped insulated electrical wiring cannot be overstated. Regular inspection and maintenance of electrical systems is crucial to identify and replace any deteriorated wiring before it poses a safety hazard. In older buildings where cloth wrapped insulated electrical wiring is still present, it is highly recommended to have it inspected by a qualified electrician to ensure its safety and reliability.
Modern Replacements
The transition from cloth wrapped insulated electrical wiring to modern replacements like PVC and rubber was driven by the need for improved insulation and safety in electrical systems. Cloth, while providing some degree of insulation and fire resistance, had limitations that posed safety concerns over time. The adoption of advanced materials like PVC and rubber addressed these limitations and significantly enhanced the safety and reliability of electrical wiring.
PVC (polyvinyl chloride) and rubber offer superior insulation properties compared to cloth. They provide a more effective barrier against electrical current, reducing the risk of electrical shocks and short circuits. Additionally, these materials are less susceptible to deterioration and moisture absorption, ensuring long-term reliability and safety. The use of PVC and rubber also allows for the production of wiring with smaller diameters, making it easier to install in tight spaces and reducing the overall cost of electrical installations.
The practical significance of understanding the connection between modern replacements and cloth wrapped insulated electrical wiring lies in the importance of electrical safety. By recognizing the limitations of cloth insulation and the advantages of modern materials, we can make informed decisions when it comes to electrical wiring and maintenance. This understanding helps prevent electrical accidents, ensures the reliable operation of electrical systems, and contributes to a safer living and working environment.
Steps to Create a Chart or Diagram of “Cloth Wrapped Insulated Electrical Wiring”
A chart or diagram of “cloth wrapped insulated electrical wiring” can be a valuable tool for understanding the construction and properties of this type of wiring. It can also be used to illustrate the steps involved in installing and maintaining cloth wrapped insulated electrical wiring.
There are a number of different ways to create a chart or diagram of cloth wrapped insulated electrical wiring. One common approach is to use a table to list the different components of the wiring, along with their dimensions and properties. Another approach is to use a diagram to show the relationships between the different components of the wiring. Regardless of the approach you choose, it is important to be clear and concise in your presentation.
The following are some tips for creating a chart or diagram of cloth wrapped insulated electrical wiring:
- Use clear and concise language. Avoid using jargon or technical terms that your audience may not be familiar with.
- Be consistent in your use of terminology. Use the same terms to refer to the same components throughout your chart or diagram.
- Use visual aids to illustrate your points. Charts, diagrams, and images can help to make your information more understandable.
- Proofread your work carefully. Make sure that your chart or diagram is free of errors before you share it with others.
Once you have created a chart or diagram of cloth wrapped insulated electrical wiring, you can use it to illustrate the steps involved in installing and maintaining this type of wiring. You can also use it to compare cloth wrapped insulated electrical wiring to other types of wiring.
Frequently Asked Questions About Cloth Wrapped Insulated Electrical Wiring
Cloth wrapped insulated electrical wiring was commonly used in the early days of electrical installations but has since been replaced by more modern materials. Nonetheless, it’s still essential to understand the properties and applications of this type of wiring, especially in older buildings.
Question 1: What is cloth wrapped insulated electrical wiring?
Answer: Cloth wrapped insulated electrical wiring is a type of electrical wiring that has an insulating layer of cloth wrapped around the conducting wires. This type of wiring was commonly used in the early days of electrical installations, but has since been replaced by more modern and safer materials such as PVC or rubber.
Question 2: What are the advantages of using cloth wrapped insulated electrical wiring?
Answer: Cloth wrapped insulated electrical wiring has several advantages, including:
- Flexibility
- Durability
- Fire resistance
Question 3: What are the disadvantages of using cloth wrapped insulated electrical wiring?
Answer: Cloth wrapped insulated electrical wiring also has some disadvantages, including:
- Susceptibility to moisture and damage over time
- Inferior insulation compared to modern materials
Question 4: Is cloth wrapped insulated electrical wiring still used today?
Answer: Cloth wrapped insulated electrical wiring is no longer commonly used in new electrical installations. However, it may still be found in older buildings and historical structures.
Question 5: What should I do if I have cloth wrapped insulated electrical wiring in my home?
Answer: If you have cloth wrapped insulated electrical wiring in your home, it is important to have it inspected by a qualified electrician. The electrician can assess the condition of the wiring and make recommendations for repair or replacement.
Question 6: How can I prevent electrical hazards from cloth wrapped insulated electrical wiring?
Answer: There are a few things you can do to prevent electrical hazards from cloth wrapped insulated electrical wiring:
- Have the wiring inspected regularly by a qualified electrician.
- Avoid overloading circuits.
- Do not use damaged or frayed wiring.
- Keep the wiring away from heat sources.
Summary: Cloth wrapped insulated electrical wiring was once widely used but has been replaced by more modern materials due to safety concerns. However, it may still be found in older buildings and historical structures. If you have cloth wrapped insulated electrical wiring in your home, it is important to have it inspected regularly by a qualified electrician.
Transition to the next article section: For more information on electrical safety, please see our other articles on the subject.
Conclusion
Cloth wrapped insulated electrical wiring played a significant role in the development of electrical systems. It provided insulation and protection against electrical hazards, enabling the safe and widespread use of electricity. However, due to its limitations and safety concerns, it has been replaced by more modern materials like PVC and rubber.
Understanding the properties and applications of cloth wrapped insulated electrical wiring is still important, especially in the context of older buildings and historical structures. Regular inspection and maintenance of this type of wiring are crucial to ensure electrical safety and prevent potential hazards. By recognizing the advancements made in electrical insulation and safety, we can appreciate the role that cloth wrapped insulated electrical wiring played in the past and the importance of using modern materials in contemporary electrical installations.
Youtube Video:
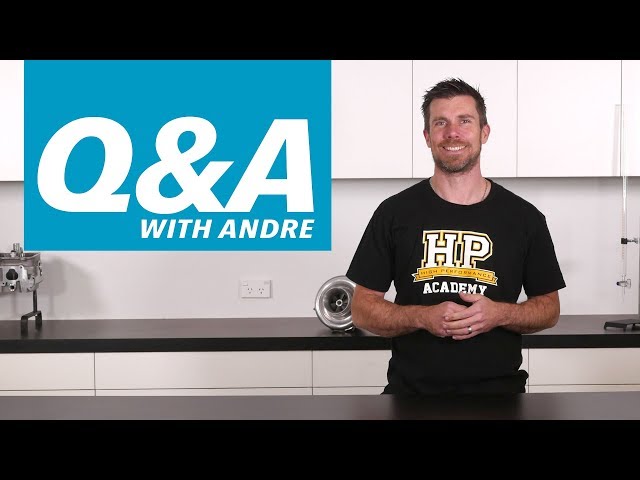