An encoder wiring diagram for a PowerFlex drive is a detailed visual guide that shows how to connect an encoder to the drive. Encoders are devices that measure the speed and position of a rotating shaft, and they are used in a variety of applications, such as robotics, automation, and motion control. The wiring diagram for an encoder will typically include information on the following:
- The type of encoder being used
- The pinout of the encoder connector
- The wiring connections between the encoder and the drive
- The electrical specifications of the encoder
Proper wiring of an encoder is critical to ensure that the drive functions correctly. If the encoder is not wired correctly, the drive may not be able to accurately measure the speed and position of the shaft, which can lead to errors in motion control and safety hazards. To connect the encoder properly, follow the wiring diagram carefully and use the correct wiring materials and tools.
encoder wiring diagram powerflex
An encoder wiring diagram for a PowerFlex drive is a detailed visual guide that shows how to connect an encoder to the drive. Encoders are devices that measure the speed and position of a rotating shaft, and they are used in a variety of applications, such as robotics, automation, and motion control. An encoder wiring diagram may include:
- Type of encoder
- Pinout of encoder connector
- Wiring connections
- Electrical specifications
- Proper wiring
- Safety hazards
These aspects are important because they ensure that the drive functions correctly and safely. If the encoder is not wired correctly, the drive may not be able to accurately measure the speed and position of the shaft, which can lead to errors in motion control. To connect the encoder properly, follow the wiring diagram carefully and use the correct wiring materials and tools.
Type of encoder
The type of encoder used in a PowerFlex drive application will determine the specific wiring diagram that is required. Encoders are typically classified into two main types: incremental encoders and absolute encoders.
- Incremental encoders measure the change in position of a rotating shaft, but they do not provide any information about the absolute position of the shaft. This type of encoder is typically used in applications where only the relative motion of the shaft is important, such as in a conveyor system or a robot arm.
- Absolute encoders measure the absolute position of a rotating shaft, providing a unique code for each position. This type of encoder is typically used in applications where it is important to know the exact position of the shaft, such as in a CNC machine or a medical imaging system.
When selecting an encoder for a PowerFlex drive application, it is important to consider the following factors:
- The required resolution of the encoder
- The required accuracy of the encoder
- The required speed of the encoder
- The environmental conditions in which the encoder will be used
Once the type of encoder has been selected, the appropriate wiring diagram can be used to connect the encoder to the drive.
Pinout of encoder connector
The pinout of an encoder connector defines the assignment of signals to the individual pins of the connector. It is important to ensure that the encoder is wired correctly to the drive, according to the pinout diagram, to ensure proper operation. Incorrect wiring can lead to damage to the encoder or the drive, or it can cause the drive to operate incorrectly.
The pinout diagram for an encoder will typically include the following information:
- The pin numbers
- The signal names
- The wire colors
When wiring an encoder to a PowerFlex drive, it is important to use the correct type of cable and connectors. The cable should be shielded to prevent electrical noise from interfering with the encoder signals. The connectors should be securely fastened to prevent them from coming loose.
By following the pinout diagram carefully and using the correct wiring materials and tools, you can ensure that your encoder is wired correctly to the PowerFlex drive. This will help to ensure that the drive operates correctly and safely.
Wiring connections
Wiring connections are an essential part of an encoder wiring diagram for a PowerFlex drive. The wiring connections define how the encoder is connected to the drive, and they must be made correctly in order for the encoder to function properly.
The wiring connections for an encoder will typically include the following:
- The power connections
- The ground connections
- The signal connections
The power connections provide power to the encoder. The ground connections provide a reference point for the encoder signals. The signal connections carry the encoder signals to the drive.
It is important to use the correct type of wire for the wiring connections. The wire should be shielded to prevent electrical noise from interfering with the encoder signals. The wire should also be the correct gauge for the current that will be flowing through it.
Once the wiring connections have been made, it is important to test the encoder to make sure that it is functioning properly. The encoder can be tested by using a voltmeter to measure the voltage at the encoder output terminals.
By following the encoder wiring diagram carefully and using the correct wiring materials and tools, you can ensure that the wiring connections for your encoder are made correctly. This will help to ensure that the encoder functions properly and provides accurate feedback to the PowerFlex drive.
Electrical specifications
Electrical specifications are an essential part of an encoder wiring diagram for a PowerFlex drive. They define the electrical characteristics of the encoder, such as its voltage, current, and power consumption. These specifications must be taken into account when selecting an encoder and wiring it to the drive.
- Voltage: The voltage of the encoder must be compatible with the voltage of the drive. The encoder wiring diagram will typically specify the voltage range that the encoder can accept.
- Current: The current draw of the encoder must be within the capacity of the drive. The encoder wiring diagram will typically specify the maximum current that the encoder can draw.
- Power consumption: The power consumption of the encoder must be taken into account when selecting a power supply for the drive. The encoder wiring diagram will typically specify the power consumption of the encoder.
- Wiring: The encoder wiring diagram will typically include a diagram of the encoder’s electrical connections. This diagram will show the pinout of the encoder connector and the wiring connections between the encoder and the drive.
By following the electrical specifications and wiring diagram carefully, you can ensure that your encoder is properly connected to the PowerFlex drive. This will help to ensure that the drive operates correctly and safely.
Proper wiring
Proper wiring is essential for the safe and reliable operation of any electrical system, including those that use encoder wiring diagrams for PowerFlex drives. An encoder wiring diagram provides a visual guide to the electrical connections between an encoder and a drive, and it is important to follow the diagram carefully to ensure that the connections are made correctly.
- Correct wire gauge: Using the correct wire gauge is important to ensure that the wires can carry the required current without overheating. The encoder wiring diagram will typically specify the minimum wire gauge that can be used for each connection.
- Properly terminated wires: All wires should be properly terminated to prevent them from coming loose or shorting out. The encoder wiring diagram will typically specify the type of termination that should be used for each connection.
- Secure connections: All connections should be secure to prevent them from coming loose. The encoder wiring diagram will typically specify the torque that should be applied to each connection.
- Proper grounding: Proper grounding is essential to protect the encoder and the drive from electrical surges and other hazards. The encoder wiring diagram will typically specify the grounding requirements for the system.
By following these guidelines, you can ensure that your encoder is properly wired to the PowerFlex drive. This will help to ensure that the drive operates correctly and safely.
Safety hazards
Improper wiring of an encoder can lead to safety hazards such as electrical fires, shock, and equipment damage. This is why it is important to follow the encoder wiring diagram carefully and use the correct wiring materials and tools.
-
Electrical fires
Electrical fires can occur if the encoder is not properly grounded or if the wiring is damaged. This can lead to serious injury or property damage.
-
Electrical shock
Electrical shock can occur if the encoder is not properly insulated or if the wiring is damaged. This can lead to serious injury or even death.
-
Equipment damage
Equipment damage can occur if the encoder is not properly wired or if the wiring is damaged. This can lead to costly repairs or even replacement of the equipment.
By following the encoder wiring diagram carefully and using the correct wiring materials and tools, you can help to prevent safety hazards and ensure the safe operation of your equipment.
Creating an encoder wiring diagram for a PowerFlex drive
An encoder wiring diagram is a detailed visual guide that shows how to connect an encoder to a PowerFlex drive. Encoders are devices that measure the speed and position of a rotating shaft, and they are used in a variety of applications, such as robotics, automation, and motion control. An encoder wiring diagram will typically include the following information:
- The type of encoder being used
- The pinout of the encoder connector
- The wiring connections between the encoder and the drive
- The electrical specifications of the encoder
Creating an encoder wiring diagram is a relatively simple process, but it is important to follow the steps carefully to ensure that the diagram is accurate and complete.
FAQs
This section provides answers to frequently asked questions about encoder wiring diagrams for PowerFlex drives.
Question 1: What is an encoder wiring diagram?
An encoder wiring diagram is a detailed visual guide that shows how to connect an encoder to a PowerFlex drive. Encoders are devices that measure the speed and position of a rotating shaft, and they are used in a variety of applications, such as robotics, automation, and motion control. An encoder wiring diagram will typically include information on the type of encoder being used, the pinout of the encoder connector, the wiring connections between the encoder and the drive, and the electrical specifications of the encoder.
Question 2: Why is it important to use an encoder wiring diagram?
Using an encoder wiring diagram is important to ensure that the encoder is connected to the drive correctly. If the encoder is not wired correctly, the drive may not be able to accurately measure the speed and position of the shaft, which can lead to errors in motion control and safety hazards.
Question 3: How do I create an encoder wiring diagram?
Creating an encoder wiring diagram is a relatively simple process, but it is important to follow the steps carefully to ensure that the diagram is accurate and complete. The steps involved in creating an encoder wiring diagram are as follows:
- Gather the necessary information. This includes the type of encoder being used, the pinout of the encoder connector, and the wiring connections between the encoder and the drive.
- Draw a schematic diagram of the wiring connections. This diagram should show the power connections, the ground connections, and the signal connections.
- Label the wires and terminals. This will help to ensure that the diagram is easy to understand and follow.
- Check the diagram for accuracy. This includes checking the pinout of the encoder connector, the wiring connections, and the electrical specifications of the encoder.
Question 4: What are some common mistakes to avoid when creating an encoder wiring diagram?
Some common mistakes to avoid when creating an encoder wiring diagram include:
- Using the wrong type of encoder.
- Wiring the encoder incorrectly.
- Not using the correct wire gauge.
- Not properly terminating the wires.
- Not following the encoder manufacturer’s instructions.
Question 5: Where can I find more information about encoder wiring diagrams?
There are a number of resources available online that can provide more information about encoder wiring diagrams. These resources include the following:
- PowerFlex Drives User Manual
- Encoder Wiring Diagrams for PowerFlex Drives
- How to Create an Encoder Wiring Diagram
Summary
Encoder wiring diagrams are an important tool for ensuring that encoders are connected to PowerFlex drives correctly. By following the steps outlined in this FAQ, you can create an accurate and complete encoder wiring diagram that will help to ensure the safe and reliable operation of your drive.
Next Steps
If you have any further questions about encoder wiring diagrams, please consult the resources listed above or contact a qualified electrician.
Conclusion
Encoder wiring diagrams are an essential tool for ensuring the proper and safe operation of PowerFlex drives. By following the steps outlined in this article, you can create an accurate and complete encoder wiring diagram that will help to ensure that your drive operates correctly and reliably.
Remember, encoder wiring diagrams are not just a collection of lines and symbols. They are a critical part of the design and implementation of any motion control system. By taking the time to create an accurate and complete encoder wiring diagram, you can help to ensure the success of your project.
Youtube Video:
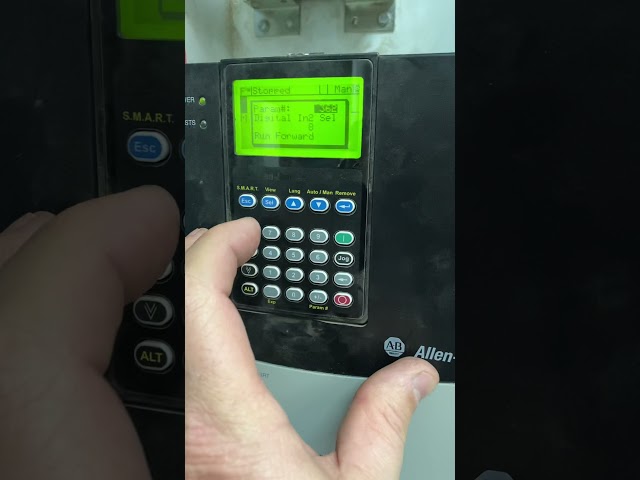