Wiring harness connector pins are electrical components that facilitate secure and efficient connections within a wiring harness, a crucial part of electrical systems in various industries, including automotive, aerospace, and telecommunications. These pins are designed to establish reliable electrical pathways between wires and connectors, ensuring the proper functioning of electronic systems.
The significance of wiring harness connector pins lies in their ability to provide consistent and dependable electrical connections. They are engineered to withstand environmental factors such as vibration, temperature fluctuations, and exposure to moisture, ensuring uninterrupted signal transmission and preventing malfunctions. Furthermore, these pins play a vital role in reducing downtime and maintenance costs by promoting system reliability and longevity.
In the main article, we will delve deeper into the types of wiring harness connector pins, their applications, and the standards governing their design and manufacturing. We will also explore the latest advancements in connector technology and discuss best practices for their installation and maintenance. This comprehensive overview will provide a thorough understanding of wiring harness connector pins and their critical role in modern electrical systems.
Wiring Harness Connector Pins
Wiring harness connector pins are crucial components in electrical systems, ensuring reliable and efficient connections. Here are seven key aspects that define their significance:
- Connectivity: Establishing secure electrical pathways between wires and connectors.
- Durability: Withstanding environmental factors such as vibration, temperature fluctuations, and moisture.
- Reliability: Maintaining consistent and dependable electrical connections.
- Variety: Available in different types and sizes to suit various applications.
- Standardization: Adhering to industry standards for design and manufacturing.
- Cost-effectiveness: Reducing downtime and maintenance costs by promoting system reliability.
- Innovation: Continuous advancements in connector technology for improved performance and efficiency.
In summary, wiring harness connector pins are essential components that ensure the proper functioning of electrical systems. Their durability, reliability, and cost-effectiveness make them indispensable in industries such as automotive, aerospace, and telecommunications. As technology continues to evolve, these pins will play an increasingly critical role in the development of more sophisticated and efficient electrical systems.
Connectivity
In the context of wiring harness connector pins, connectivity refers to the ability of these pins to establish secure and reliable electrical pathways between wires and connectors. This is a fundamental aspect of their function, as it ensures the proper flow of electrical signals and power throughout the system.
- Types of Connections: Wiring harness connector pins come in various types, each designed for specific applications. These include crimp pins, solder pins, and insulation displacement pins, among others. The choice of pin type depends on factors such as the wire size, current carrying capacity, and environmental conditions.
- Contact Design: The contact design of the pins is crucial for ensuring a secure connection. The pins are typically designed with a spring-loaded mechanism that provides constant pressure against the wire, maintaining a low resistance connection. This prevents intermittent connections and ensures reliable signal transmission.
- Durability: Wiring harness connector pins are subjected to various environmental factors, including vibration, temperature fluctuations, and exposure to moisture. They are designed and manufactured using durable materials and coatings to withstand these conditions and maintain their integrity over the lifetime of the system.
- Standardization: Wiring harness connector pins adhere to industry standards, ensuring compatibility and interoperability between different components and systems. This standardization simplifies the design and assembly of wiring harnesses, reducing errors and increasing reliability.
In summary, the connectivity aspect of wiring harness connector pins is essential for establishing secure and reliable electrical pathways between wires and connectors. The variety of pin types, contact design, durability, and adherence to standards contribute to the overall performance and reliability of electrical systems.
Durability
The durability of wiring harness connector pins is a critical aspect of their performance and reliability. Electrical systems are often subjected to harsh environmental conditions, including vibration, temperature fluctuations, and moisture. These factors can put stress on the pins and lead to intermittent connections or even complete failure.
To ensure reliable operation, wiring harness connector pins are designed and manufactured to withstand these environmental challenges. They are typically made from durable materials such as copper alloys or stainless steel, which resist corrosion and wear. The pins are also designed with features that minimize the effects of vibration and temperature fluctuations. For example, some pins have a spring-loaded design that provides constant pressure against the wire, maintaining a secure connection even under vibration.
The durability of wiring harness connector pins is essential for the reliability of electrical systems. By withstanding environmental factors, these pins help to ensure that electrical signals are transmitted reliably and consistently, even in harsh conditions. This is critical in applications such as automotive systems, where electrical failures can have serious consequences.
Reliability
Reliability is a crucial aspect of wiring harness connector pins, as it directly impacts the overall performance and safety of electrical systems. Consistent and dependable electrical connections are essential for ensuring that electrical signals are transmitted accurately and without interruption, preventing malfunctions and system failures.
The reliability of wiring harness connector pins is achieved through several key factors:
- High-quality materials: Wiring harness connector pins are typically made from durable materials such as copper alloys or stainless steel, which resist corrosion and wear.
- Precise manufacturing: The pins are manufactured with high precision to ensure proper fit and alignment, reducing the risk of loose connections or arcing.
- Robust design: The pins are designed with features that minimize the effects of vibration, temperature fluctuations, and other environmental factors.
Reliable wiring harness connector pins are essential for a wide range of applications, including automotive systems, industrial machinery, and medical devices. In automotive systems, for example, reliable electrical connections are critical for ensuring the proper functioning of safety-critical components such as airbags, brakes, and steering systems. In medical devices, reliable connections are essential for ensuring patient safety and accurate diagnosis and treatment.
By understanding the importance of reliability in wiring harness connector pins, engineers and technicians can design and maintain electrical systems that are safe, efficient, and dependable.
Variety
The variety of wiring harness connector pins available is crucial for meeting the diverse requirements of various applications. The types and sizes of pins are carefully designed to suit specific electrical and mechanical needs, ensuring optimal performance and reliability in different environments.
For instance, in automotive applications, wiring harness connector pins are available in a range of sizes to accommodate different wire gauges and current carrying capacities. This variety ensures that the pins can handle the electrical loads of various components, from sensors and actuators to power distribution modules.
In addition to size variations, wiring harness connector pins come in different types, each with unique characteristics and applications. Crimp pins, for example, are designed for quick and efficient termination using a crimping tool, while solder pins require soldering for a more permanent connection. Insulation displacement pins, on the other hand, pierce the insulation of the wire, creating a gas-tight connection without the need for stripping or soldering.
Understanding the variety of wiring harness connector pins and their specific applications is essential for engineers and technicians. By selecting the appropriate pins for each application, they can ensure that electrical systems are safe, reliable, and meet the required performance specifications.
In summary, the variety of wiring harness connector pins available is a critical aspect of their functionality and versatility. By providing a wide range of types and sizes, these pins can be tailored to suit the unique requirements of different applications, ensuring optimal performance and reliability.
Standardization
Standardization plays a crucial role in the design and manufacturing of wiring harness connector pins, ensuring their compatibility, reliability, and interchangeability across different applications and systems.
- Compatibility and Interoperability: Adherence to industry standards ensures that wiring harness connector pins manufactured by different suppliers meet the same specifications and dimensions. This facilitates the seamless integration of components from various sources, reducing compatibility issues and simplifying system assembly.
- Improved Reliability: Industry standards define specific requirements for materials, manufacturing processes, and testing criteria. By adhering to these standards, manufacturers can ensure that wiring harness connector pins meet the highest levels of quality and reliability, minimizing the risk of failures and malfunctions.
- Simplified Maintenance and Repair: Standardized wiring harness connector pins enable easy maintenance and repair of electrical systems. Technicians can quickly identify and replace faulty pins using standard tools and procedures, reducing downtime and maintenance costs.
- Cost Reduction: Standardization allows for economies of scale in manufacturing, as suppliers can produce larger quantities of standardized components. This reduces production costs and ultimately benefits end-users by making wiring harness connector pins more affordable.
In summary, standardization is essential for the design, manufacturing, and performance of wiring harness connector pins. By adhering to industry standards, manufacturers can ensure compatibility, reliability, simplified maintenance, and cost-effectiveness, ultimately contributing to the overall quality and reliability of electrical systems.
Cost-effectiveness
The cost-effectiveness of wiring harness connector pins is directly tied to their ability to promote system reliability and reduce downtime and maintenance costs. Reliable connector pins ensure stable electrical connections, minimizing the risk of malfunctions and failures that can lead to costly repairs and system downtime.
By utilizing durable materials and robust designs, wiring harness connector pins withstand harsh operating conditions, vibration, and temperature fluctuations, ensuring long-term performance and reducing the need for frequent maintenance or replacement. This translates into significant cost savings over the lifespan of electrical systems.
Furthermore, the standardization of wiring harness connector pins simplifies maintenance procedures and reduces the need for specialized tools or training. Technicians can quickly identify and replace faulty pins, minimizing downtime and labor costs.
In summary, the cost-effectiveness of wiring harness connector pins lies in their ability to enhance system reliability, reduce downtime, and simplify maintenance. By investing in high-quality connector pins, businesses and organizations can minimize operational costs and maximize the efficiency of their electrical systems.
Innovation
In the realm of electrical systems, innovation has been a driving force behind the continuous advancements in connector technology. These advancements have had a profound impact on wiring harness connector pins, leading to improved performance and efficiency in a wide range of applications.
- Reduced Size and Weight: Advancements in materials science and manufacturing techniques have enabled the development of smaller and lighter connector pins without compromising their durability or performance. This miniaturization is particularly beneficial in industries such as aerospace and consumer electronics, where space and weight constraints are critical.
- Increased Durability: New materials and designs have enhanced the durability of connector pins, making them more resistant to wear, corrosion, and environmental factors. This is especially important in harsh operating conditions, such as those found in automotive and industrial applications.
- Improved Electrical Performance: Innovations in contact design and materials have led to improved electrical performance of connector pins. They now offer lower contact resistance, higher current carrying capacity, and reduced signal loss, ensuring reliable and efficient signal transmission.
- Simplified Assembly and Maintenance: Connector manufacturers have focused on simplifying the assembly and maintenance of wiring harnesses by developing user-friendly designs and tools. This reduces installation time, minimizes errors, and facilitates troubleshooting, ultimately saving time and costs.
These advancements in connector technology have revolutionized the design and performance of wiring harness connector pins. By embracing innovation, manufacturers have created pins that are more compact, durable, efficient, and easier to use. These improvements have contributed to the overall reliability, cost-effectiveness, and versatility of electrical systems across various industries.
Creating Wiring Harness Connector Pin Charts and Diagrams
Wiring harness connector pin charts and diagrams are essential tools for designing, assembling, and maintaining electrical systems. They provide a visual representation of the pin layout, making it easier to understand and troubleshoot connections.
There are several types of charts and diagrams that can be used to represent wiring harness connector pins. Some of the most common include:
- Pinout Diagrams: These diagrams show the arrangement of pins within a connector, including their numbers, functions, and wire colors.
- Wiring Diagrams: These diagrams show how the pins in a connector are connected to other components in the system.
- Schematics: These diagrams provide a more detailed view of the electrical system, including the pinouts, wiring, and other components.
To create a wiring harness connector pin chart or diagram, follow these steps:
- Identify the connector: Determine the type of connector being used and the number of pins it has.
- Gather information: Collect information about the function of each pin, including its wire color and termination type.
- Create a layout: Sketch out the arrangement of the pins within the connector.
- Label the pins: Assign numbers or labels to each pin based on its function.
- Draw the diagram: Use a drawing tool or software to create a clear and accurate diagram of the connector pin layout.
Wiring harness connector pin charts and diagrams are valuable tools for ensuring the proper assembly and maintenance of electrical systems. By following these steps, you can create clear and accurate diagrams that will help you to identify and troubleshoot problems quickly and efficiently.
FAQs on Wiring Harness Connector Pins
Wiring harness connector pins play a crucial role in the functionality and reliability of electrical systems. Here are answers to some frequently asked questions about these essential components:
Question 1: What are the different types of wiring harness connector pins?
Answer: Wiring harness connector pins come in various types, including crimp pins, solder pins, insulation displacement pins, and hermaphroditic pins. Each type has its unique design and application.
Question 2: How do I choose the right wiring harness connector pins?
Answer: The selection of wiring harness connector pins depends on factors such as the wire size, current carrying capacity, environmental conditions, and the type of connection required.
Question 3: How do I ensure a secure connection with wiring harness connector pins?
Answer: Proper installation is crucial for secure connections. Use the correct crimping tool or soldering technique based on the pin type. Ensure that the wires are stripped to the appropriate length and inserted fully into the pins.
Question 4: What are the common causes of wiring harness connector pin failure?
Answer: Common causes include corrosion, vibration, improper installation, and exposure to harsh environmental conditions.
Question 5: How can I troubleshoot wiring harness connector pin problems?
Answer: Troubleshooting involves visual inspection for damage, checking for loose connections, and testing for continuity using a multimeter.
Question 6: What are the latest trends in wiring harness connector pin technology?
Answer: The industry is moving towards smaller, more durable, and cost-effective connector pins. Advanced materials and manufacturing techniques are enabling these advancements.
In conclusion, wiring harness connector pins are critical components that require careful selection and proper handling. Understanding their types, applications, and potential issues can help ensure reliable and efficient electrical connections.
Transition to the next article section: Advanced Applications of Wiring Harness Connector Pins
Conclusion
Throughout this article, we have explored the critical role of wiring harness connector pins in ensuring the functionality and reliability of electrical systems. From their diverse types and applications to their importance in maintaining secure and efficient connections, we have gained a comprehensive understanding of these essential components.
As technology continues to advance, the demand for smaller, more durable, and cost-effective wiring harness connector pins will only increase. By embracing innovation and adhering to industry standards, manufacturers can create connector pins that meet the evolving needs of various industries.
In conclusion, wiring harness connector pins are the unsung heroes of electrical systems,facilitating the flow of electrical signals and power. Their reliability, versatility, and ongoing advancements make them indispensable for the development of safe, efficient, and interconnected electrical systems that shape our modern world.
Youtube Video:
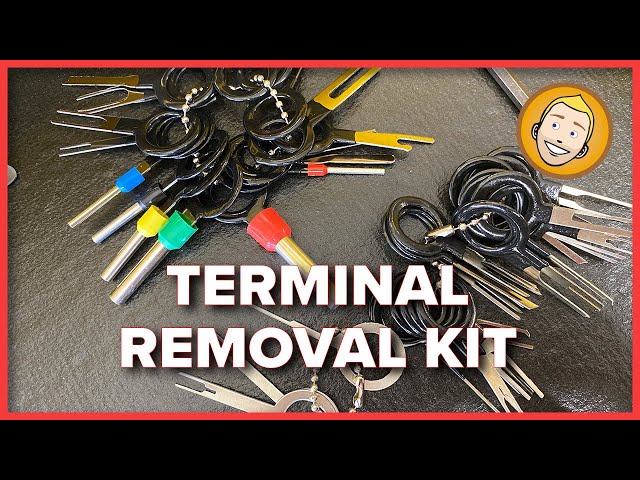